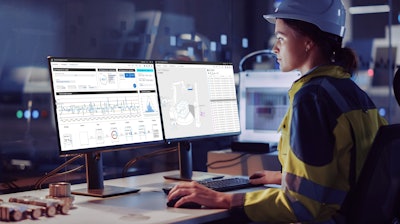
As industrial automation technologies have evolved, many system integrators and end users have become accustomed to choosing different solutions based on the size and scope of their project.
A small installation could be a single machine, a medium installation might encapsulate a few production lines with several different pieces of software, and a large installation would span through the enterprise, potentially bridging information technology and traditional operations technology software.
This kind of simplified categorization is convenient but can lead to technically and commercially constraining results due to the unwieldly variety of software employed in each category.
Modern manufacturing and production operations—whether consisting of a few pieces of equipment in a facility or many assets across numerous sites—require every advantage to achieve the highest quality and performance. Meanwhile, operators, maintenance personnel, supervisors, and managers each prioritize different industrial software functions.
Operators desire direct visibility to control machines, maintenance personnel have questions about performance, supervisors need shift data, and management strives to drive efficiency improvements.
Meeting so many needs at varying scales while leveraging the latest technology advancements is a demanding undertaking. End users, original equipment manufacturers (OEMs), and systems integrators (SIs) have become accustomed to specifying and integrating many small/medium/large products to meet various needs, even though the approach is complex, costly, and often comes with risk. However, these stakeholders seek a more streamlined way to achieve comprehensive visibility and control of their operations.
AVEVA
Software can be the right size for any scale
Achieving mission-critical situational awareness of industrial operations requires various software components such as human-machine interfaces (HMIs), supervisory control and data acquisition (SCADA) systems, historians, and tools for alarming and reporting. In recent years, advanced business connectivity and data analytics capabilities have also become increasingly important.
The best solution for supporting day-to-day needs for all stakeholders in manufacturing and production enterprises of any size is to choose a proven suite of industrial operations control software built from the ground up to integrate all requirements cleanly. This enables designers to invest their time in developing high-performance solutions for end users, line managers, and leaders instead of expending effort investigating and testing a multitude of possibly useful products that may not play well together.
Licensing, deployment, and functionality
Specifiers need to ensure the visualization software suite addresses the development, deployment, production, and support phases. Flexibility for procuring the software, deploying it, and obtaining the desired functionality on demand must all be considered.
Licensing
Platforms employing commercial models based on hard-to-anticipate tag counts or server point-count limitations have been a cause of great concern in recent years. Instead, developers vastly prefer models based on user licensing and subscriptions that free designers from burdensome commercial constraints, making the software easy to use from a development perspective and simple to budget for and procure from a business perspective. In a sense, implementors purchase only as much as they need on an ongoing basis.
With a single software solution to meet diverse levels of need, users can freely ramp up or even down their application licensing. Two popular capability classes include:
- Edge: Unlimited HMI Perfect solution for frontline teams that require local process monitoring and control at the asset, equipment, or line level with IIoT and embedded HMI capabilities.
- Supervisory: Ideal for centralized management of distributed SCADA or operations into single unified plant model aimed at driving standardization across departments.
Many applications start on the smaller side and then grow over time with equipment expansion. The ability and benefit of gaining capabilities by simply modifying licensing while preserving all existing development and software investments cannot be overstated.
Deployment
A complete visualization solution must be architected to scale seamlessly from the smallest to largest installations, while integrating with other aspects of the business, such as enterprise resource planning (ERP) and manufacturing execution systems (MES).
The software deployment and access methodology—whether at the edge, on-premises in the control room, in the cloud, on mobile devices, or a hybrid—should be completely transparent, and even selectable via simple checkboxes.
Furthermore, the cloud portions of any solution are reliably hosted by the software supplier, providing a reliable software update process and mitigating cybersecurity risk.
Advanced functionality beyond visualization
Standard HMI/SCADA features, such as graphical objects and data trends, are increasingly becoming a commodity and are well understood. But automation users everywhere are becoming aware of the exceptional value within the data generated by even their smallest tag-count systems, provided they can easily access the data, analyze it, gain insights, and enhance system performance. This means implementing analytics and using machine learning and generative AI tools, each of which is a significant step above conventional HMI/SCADA capabilities.
However, a complete visualization software suite provides direct and streamlined access to these capabilities when the time is right to use them. Users can leverage pre-defined and self-service editable dashboards and animations to holistically visualize complex interactions and incorporate a combination of artificial intelligence and analytics in their applications, enabling them to reduce production costs, predict potential equipment failure, and rapidly locate any information within their systems within seconds. A proven operations control software suite enables users to rapidly prototype, test, and iterate before scaling to production.
Conversely, consider possibilities outside the realm of normal HMI/SCADA applications. It is becoming practical, for example, to use generative AI assistants—advanced forms of wizards—to accelerate development and implementation tasks. This type of assistant, accessible in a visualization software suite, can provide training modules and skill-building functions to develop the workforce and provide effective knowledge capture and transfer. This software fosters team collaboration, along with hosting site documentation—such as manuals and drawings—for fast and convenient access. These capabilities are difficult to develop in-house and require a dedicated support team to keep them up and running. Unlike an all-inclusive operations software suite with built-in features such as AVEVA Operations Control.
Gain complete operational control
Larger enterprises are historically most likely to possess the resources to undertake large automation and visualization projects. However, innovative operations control software suites with simplified licensing, improved scalability, and flexible deployment options provide accessible solutions for end users, OEMs, and SIs on projects of all sizes.